Home » Our Services » Machine Safeguarding » Fonterra Collingwood St – Cheese Palletising Robots Safety Upgrade
Fonterra Collingwood St – Cheese Palletising Robots Safety Upgrade
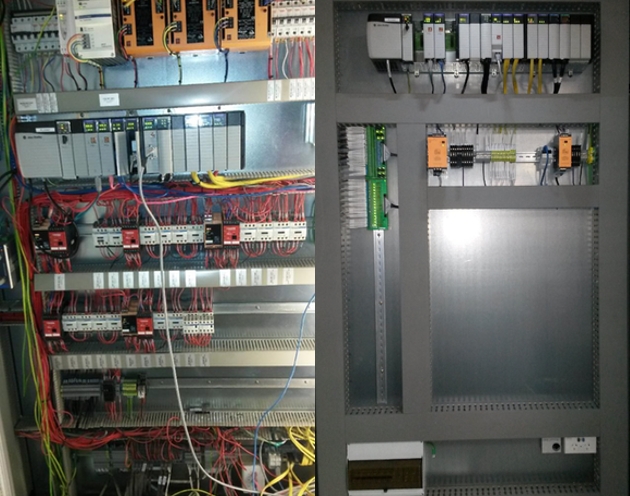
It was found historically, that the ASI safety system in use on the palletising plant was unreliable. Also it required specialist expertise to repair causing long periods of downtime.
The plant consisted of a pallet dispenser, infeed shuttle, 3x robot cells, outfeed shuttle, JMP stretch wrapper, Lantech stretch wrapper, and overflow conveyor.
This project was challenging as it involved 9 separate safety zones.
An intense verification/validation plan for functionality was required for all common mode failures due to the possibility of forced entries from various directions.
Because the plant is run 24/7 365 days a year, shut down times for installation were critical and had to be precisely planned.
Project Requirements as per Machine Risk Assessment (MRA)
- Performance Level “d” – (PL)d
- Category 3 architecture
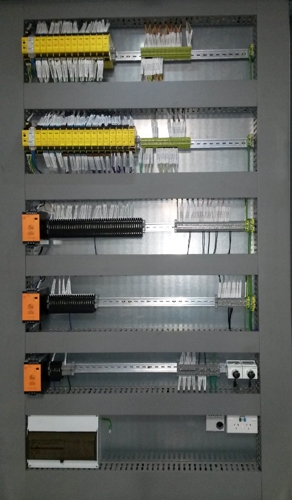
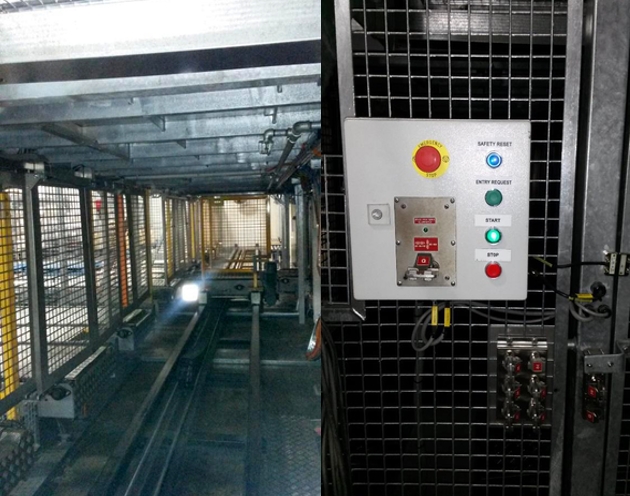